Custom screws for hydraulics
15 years of service experience in the hydraulic industry | German equivalent sealing technology | Sany Rexroth Pyke long-term partner
Why did sany choose our 5 million fatigue tests?
Full digital servo pulse tester, 1:1 reduction of dynamic load of hydraulic system
Hydraulic grade testing system
1. spectral analysis of raw materials
2. cold heading crystal phase detection
3.Metallographic verification of heat treatment
4. helium mass spectrometer leak detection of finished product
In line with ISO 10763 hydraulic pipe components international standards
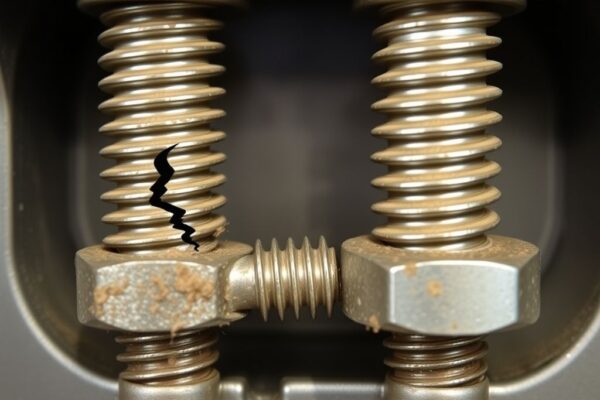
Hydraulic optimization tips
🔹 Anti-cavitation design: thread fluid dynamics optimization
🔹 Quick response: < 20 minutes to switch the mold, support small batch multi-species
🔹 Intelligent prediction: recommendation of optimal preload torque based on pressure data
Parameters | Conventional turning | Cold heading process |
Cost | ¥8.6 per piece | ¥4.2 per piece |
Production rate | 120 pieces per hour | 800 pieces per hour |
Life expectancy | 2 years | 5 years |
The process breakthrough of cartridge valve screw cost reduced by 50%
Cold heading instead of turning, surface carbon tungsten coating instead of hard chromium plating, strength and corrosion resistance double
Hydraulic pressure purchase guarantee
🔹3-year extended warranty
🔹Payment in advance for quality problems
🔹Trade-in discount for old parts
The 2023 saves hydraulic customers over 36 million yuan in maintenance costs
01.
Material cost accounted for 42%
02.
The process cost is 31%
03.
Testing cost 15%
04.
Profit 12%
Custom pricing
Free sample verification, maximum 15% refund after mass production, product price commitment signed online
Stage | Unit Price | Lead Time | Exclusive rights and interests |
Samples (1-10) | $ XX.XX | 3 days | Free of mould fee |
Small Batch (1000) | $ XX.XX | 7 days | Send the Destructive testing |
Mass production (100,000 +) | $ XX.XX | 15 days | General factory acceptance in factory |
Why Us?
We have advanced equipment and technical personnel with more production experience.
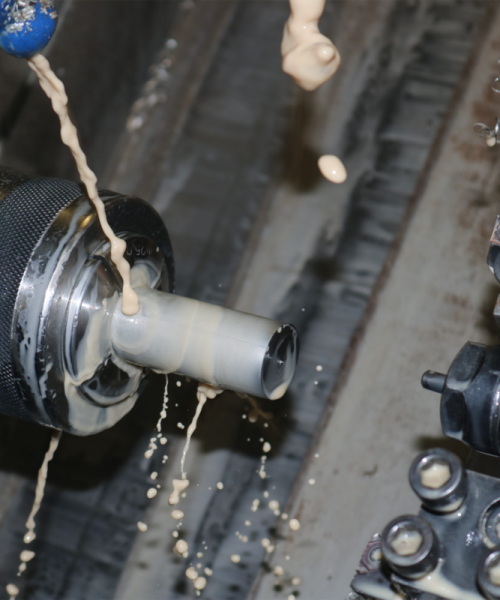
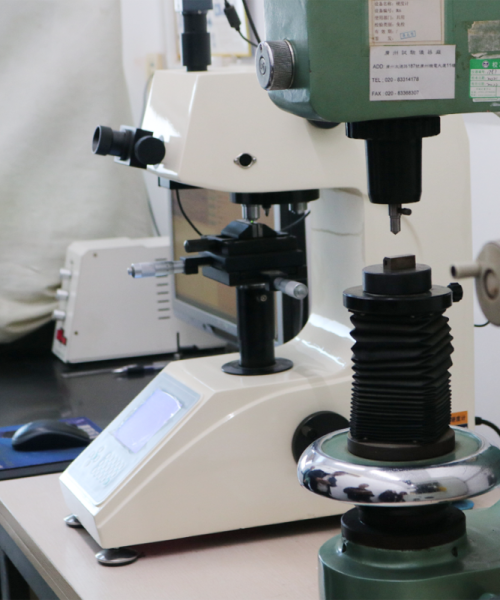
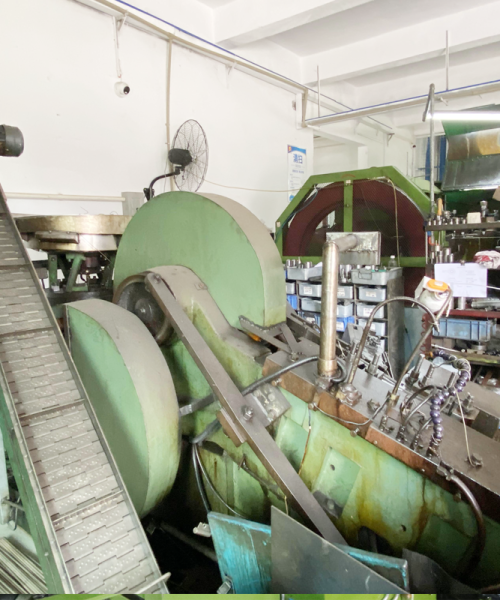
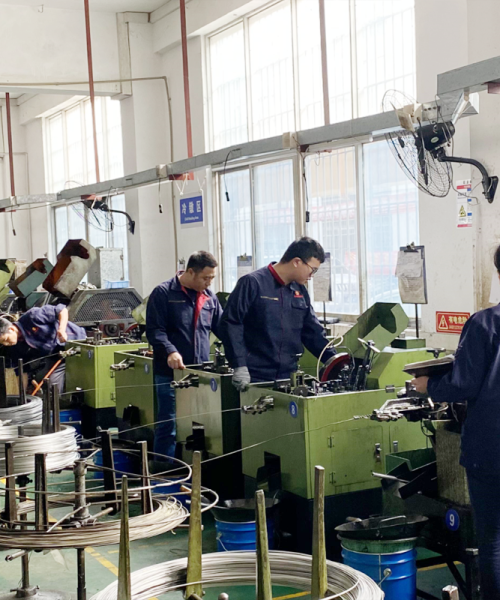
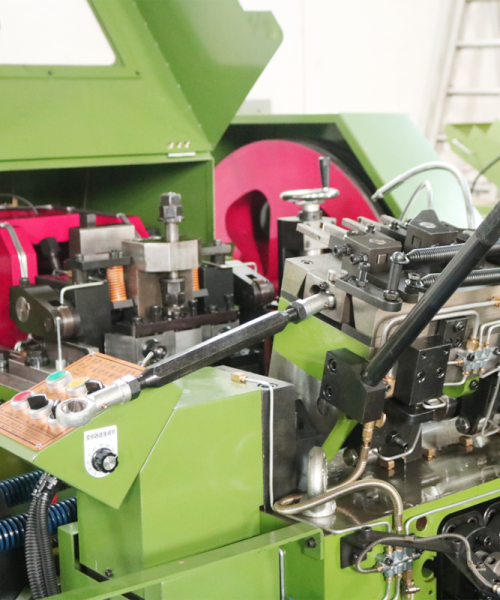
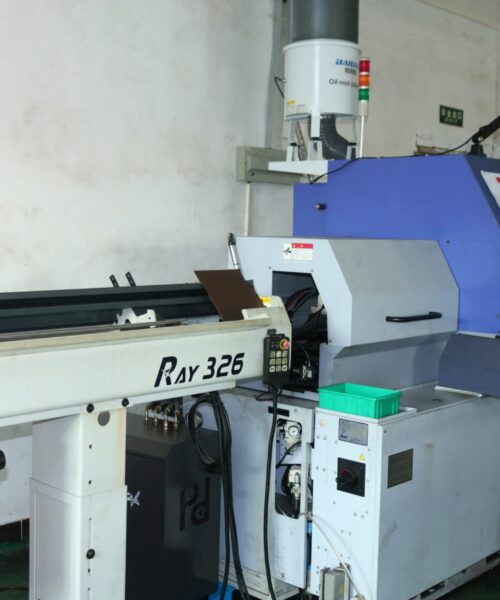
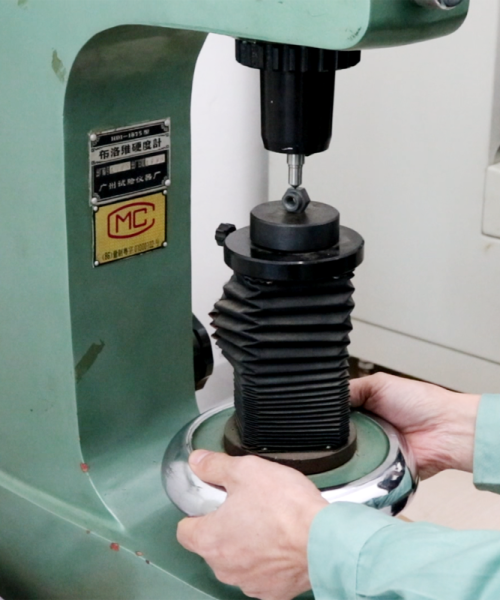
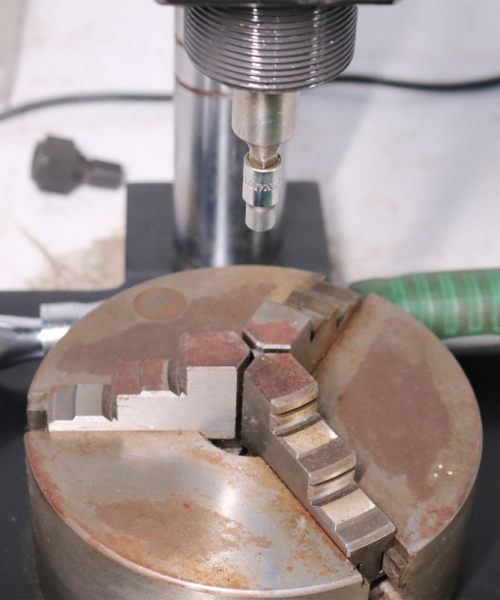
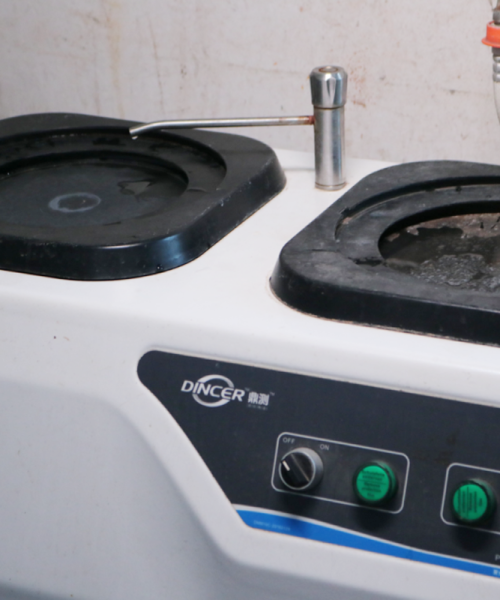
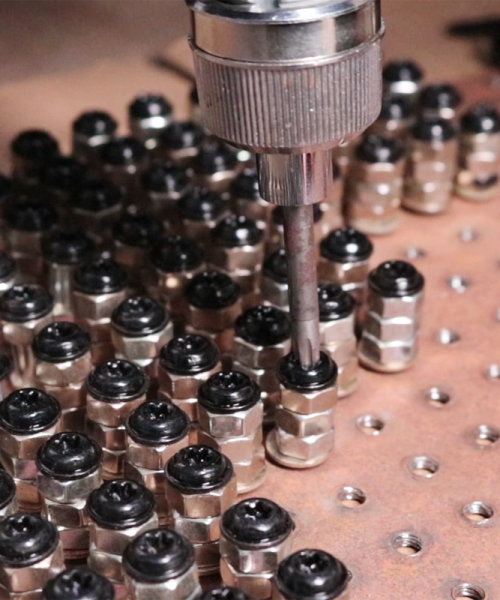
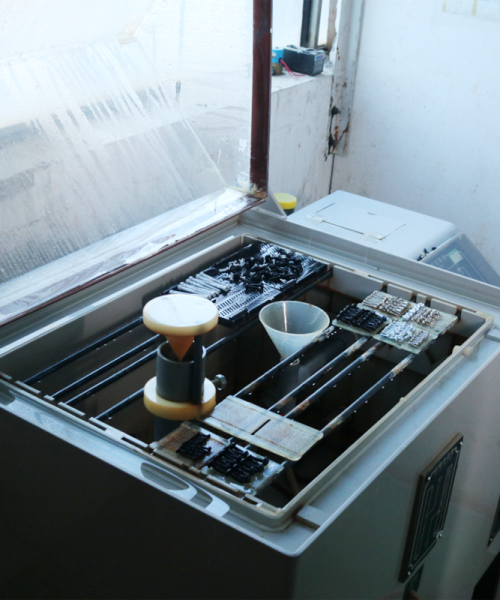
See the birth of each screw: 24-hour live broadcast clean workshop
Japan shimadzu heat treatment line + Germany Bosch tightening system, precision to DIN 13-28 standard
Hydraulic Intelligence Standard
✅ Dimensional tolerance ± 0.015 mm
✅Surface roughness Ra0.8
✅Salt spray test > 720h
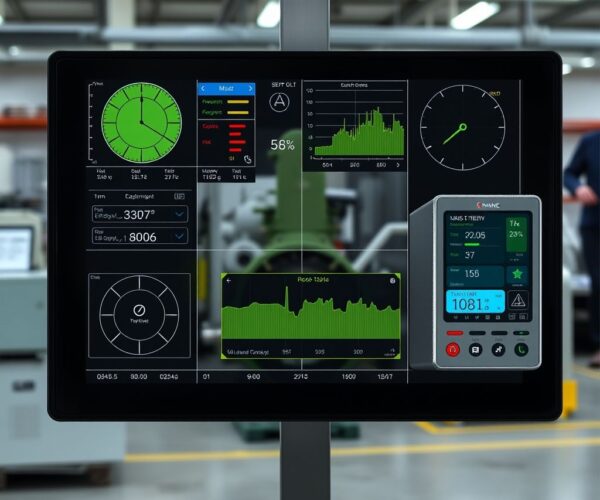
Our services
Mainly for the need for high-precision, high-performance, complex structure, personalized customized screws b-end customer service
Complexity and efficiency of procurement
One-stop supply of screws, springs, turning parts, nuts, gaskets, stamping parts, to solve the complexity of multi-party customer procurement and time costs. Urgent order on the same day, process more orders shipped within 7 days, the whole department to ensure rapid delivery, to solve the urgent problem of customer delivery.
Customized service for the whole process
From design consulting, rapid docking, technical advice to production delivery, support for personalized customization (size, material, surface treatment, special shape) .
Department-wide collaboration
The company's 94-person team division of labor is clear, for urgent orders with the whole department to ensure rapid delivery.
Factory strength support
6750 square meters factory, including screw workshop (1650 square meters, 19 people) , CNC workshop (1500 square meters, 20 people, 4/5 axis machine) , Stamping Workshop (1200 square meters, 15 sets of 50-500 tons machine) , spring workshop (1200 square meters, 14 people) .
Lack of technical support
36 years of experience as chief engineer and 14 years of average experience as a team to provide professional advice to solve customer technical problems in fastener design and material selection. Provide technical resources (E. G. Material Guides, test reports) to help engineers optimize the design.
Quick response
Simple Screw 10 minutes offer, complex screw 1 hour offer, support urgent order (try to machine the same day, process more orders shipped within 7 days) .
Data detection
We will carry out a lot of screw products sampling test, to ensure that customers get our qualified products.
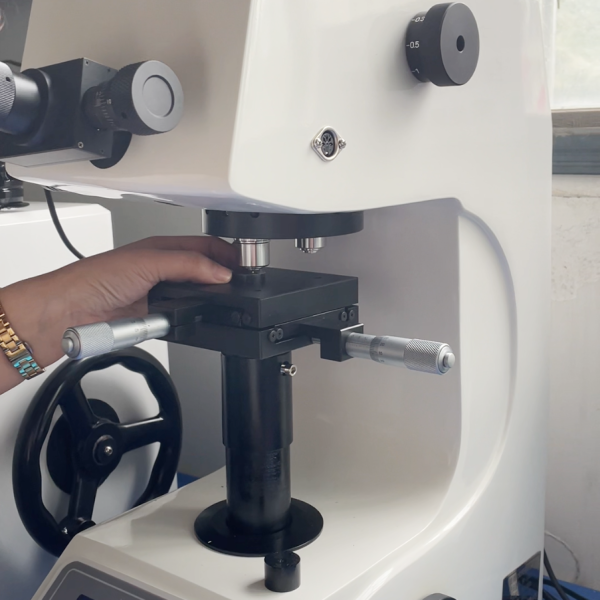
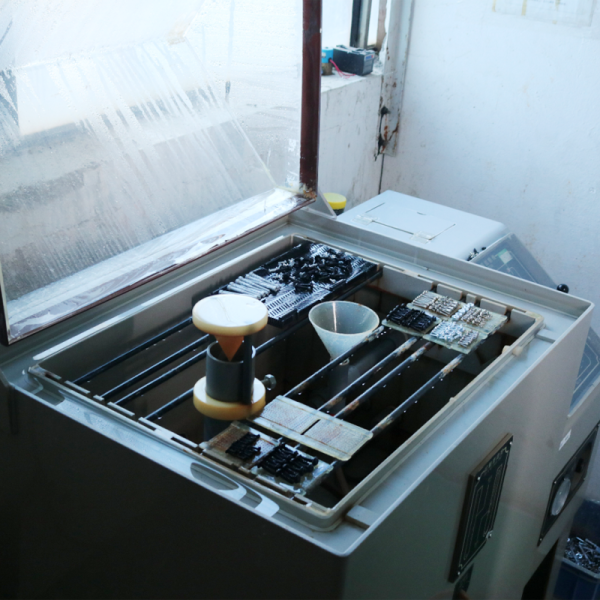
Strict quality control
36 years general work team check, 100% simulation of actual combat environment, from the source to eliminate the risk of broken head/sliding teeth.
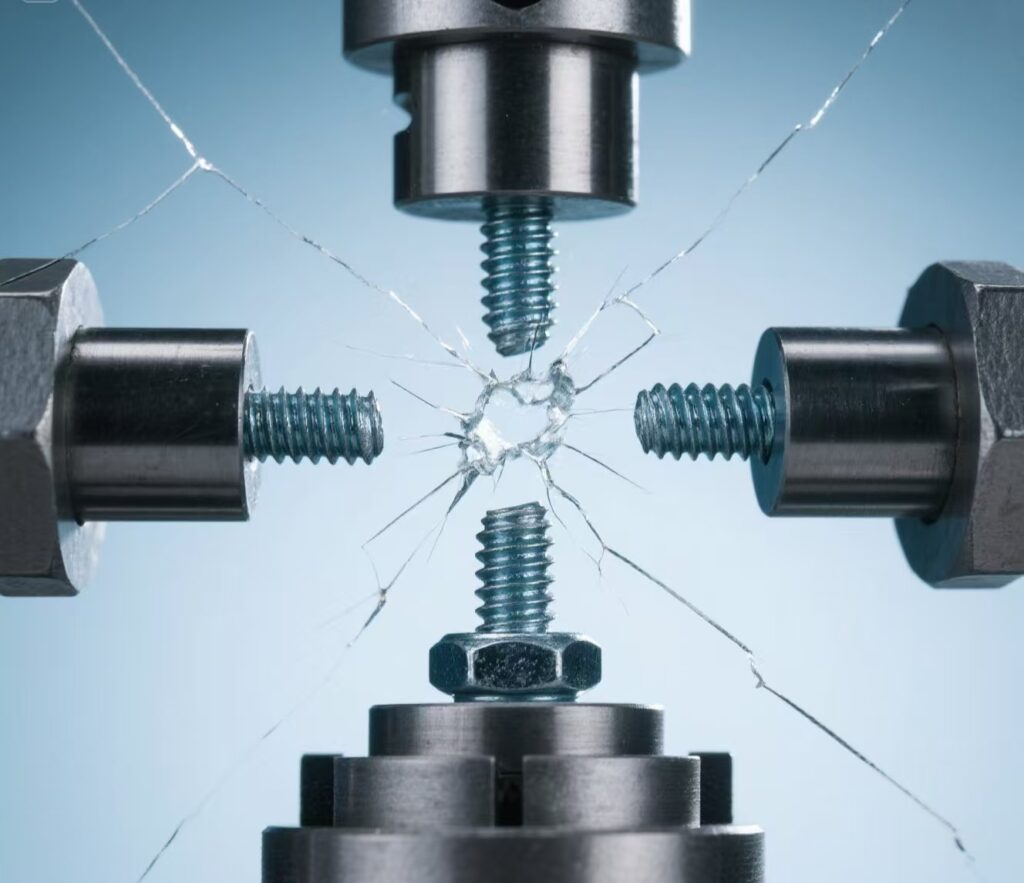
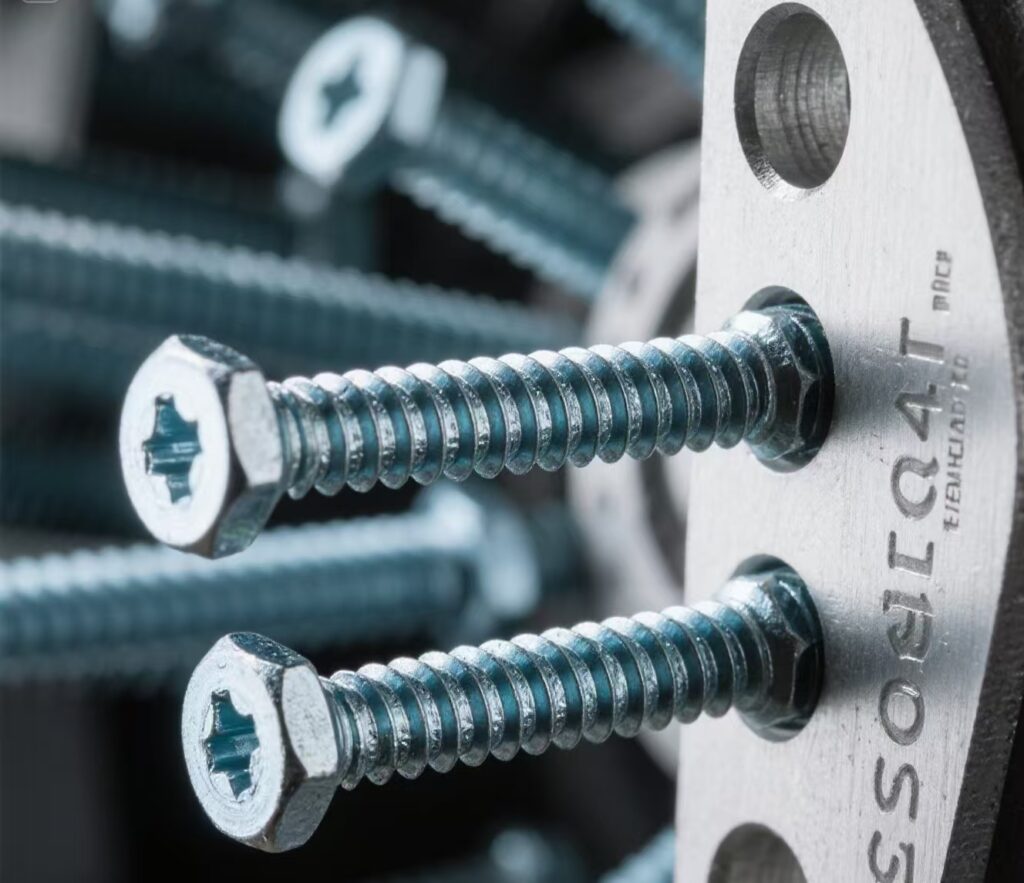
1000-hour pulse test
German Rexroth with the same type of sealing technology, thread engagement increased by 40% , eliminate hydraulic oil leakage
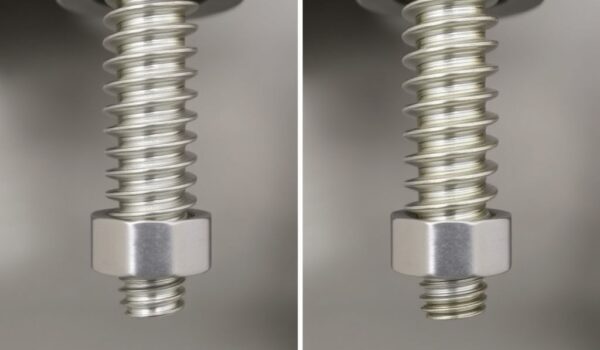
Technical Matrix of hydraulic research
🔹Anti-fretting wear: QPQ surface treatment hardness up to HRC60
🔹Anti-loosening design: pre-coated anaerobic glue + triangle tooth pattern double locking
🔹Rapid Maintenance: Unified Interface Design, maintenance time reduced by 70%
Production process
Intelligent optimization process, precision intelligent manufacturing each fastener
Products
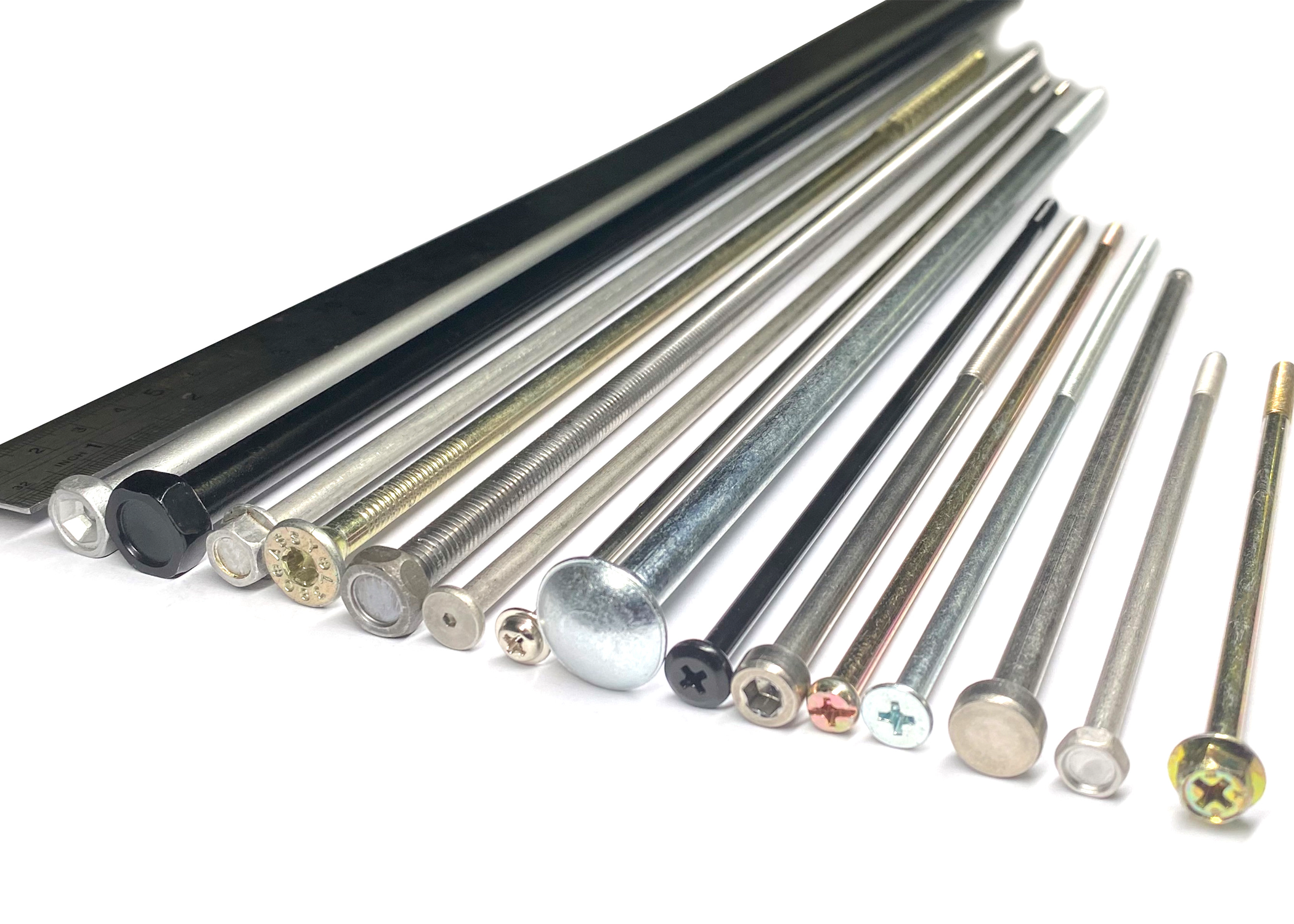
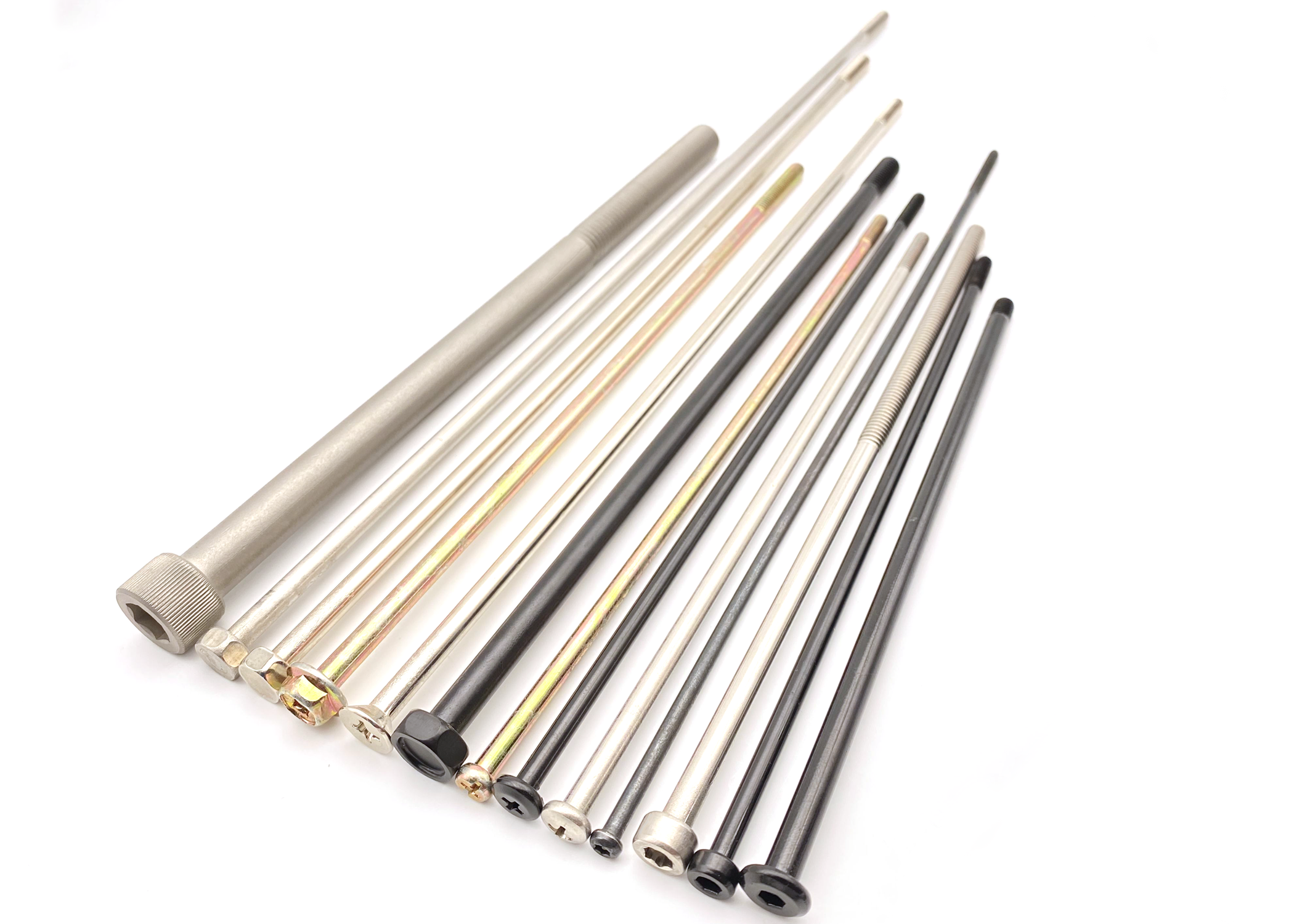
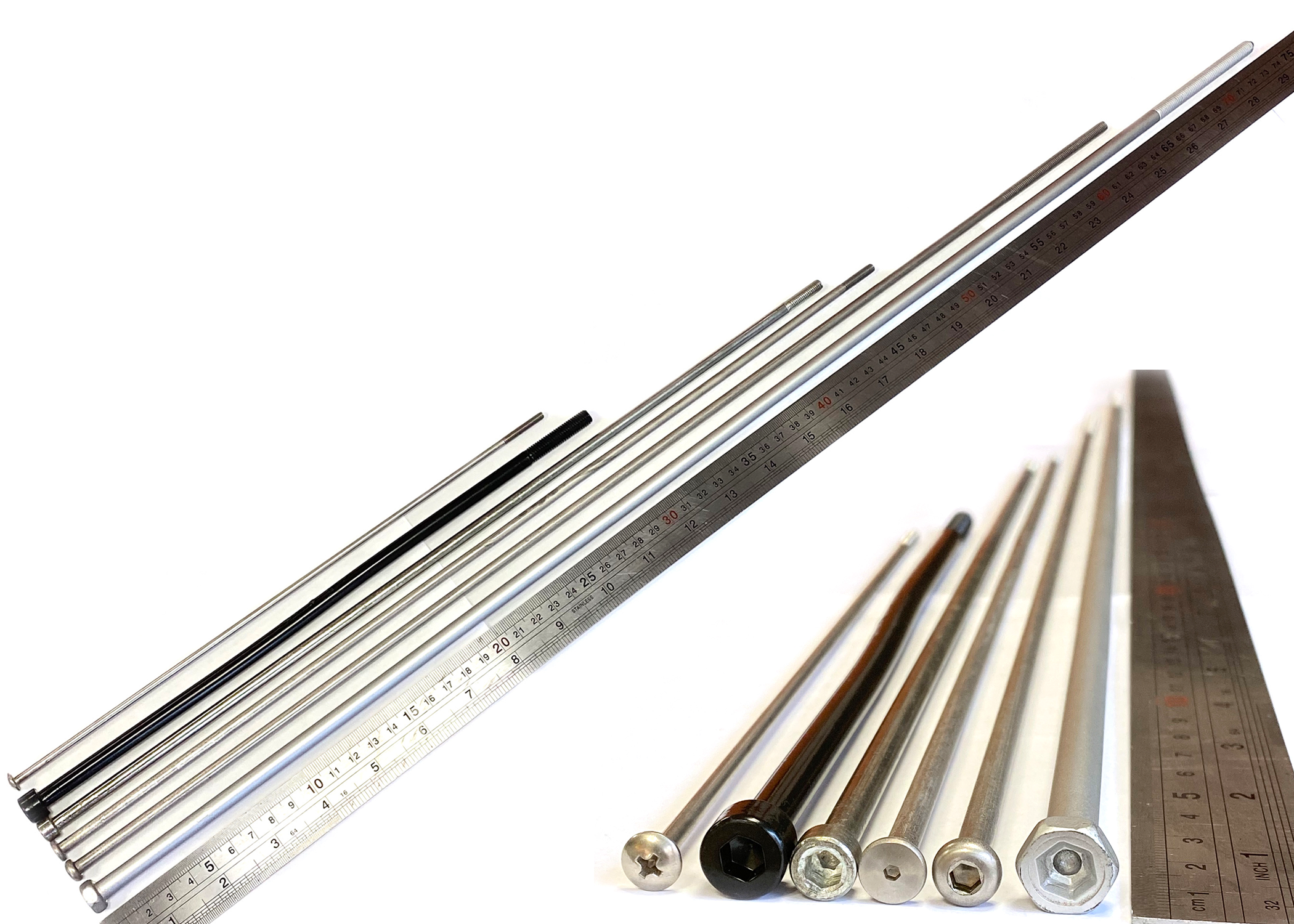
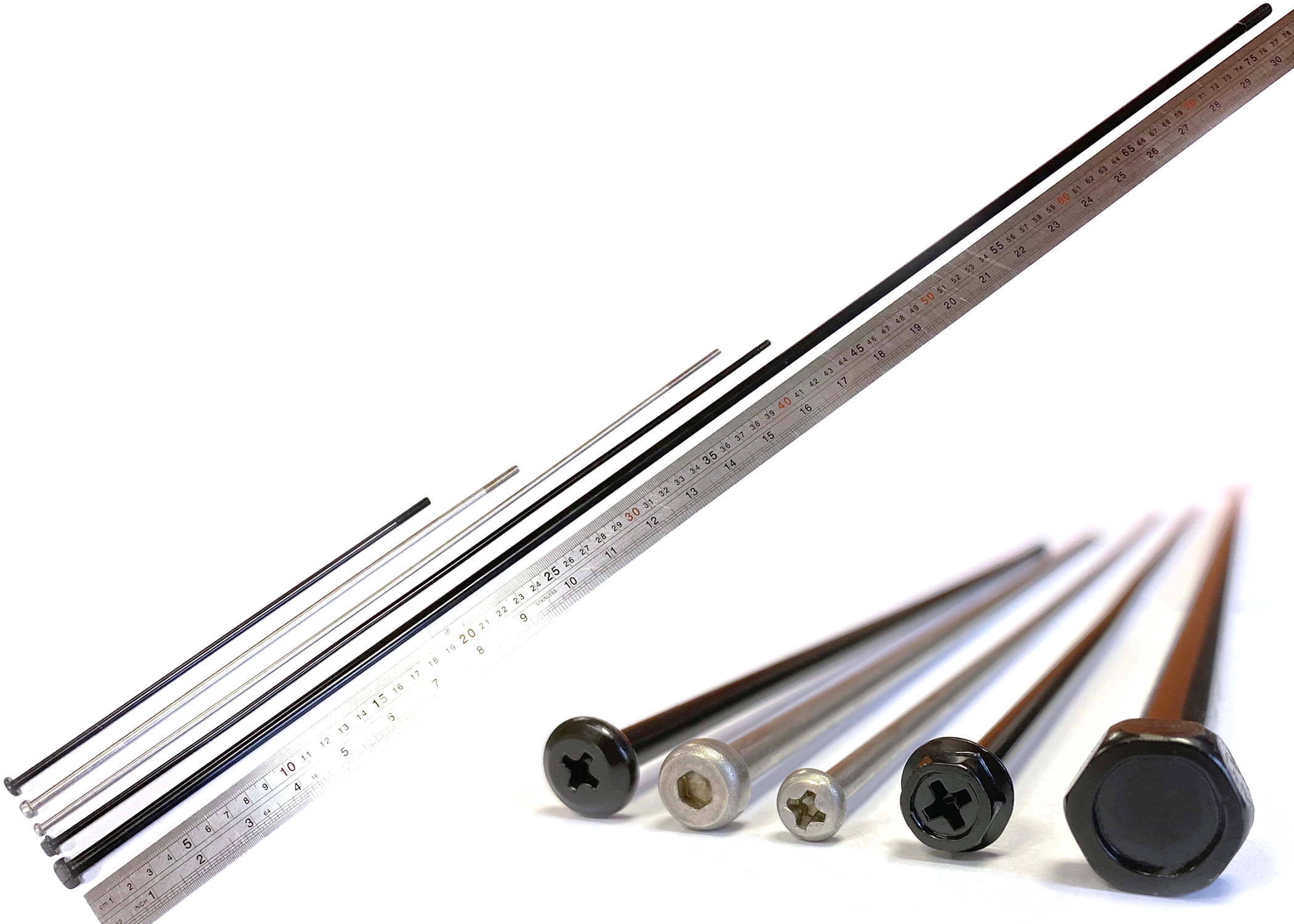
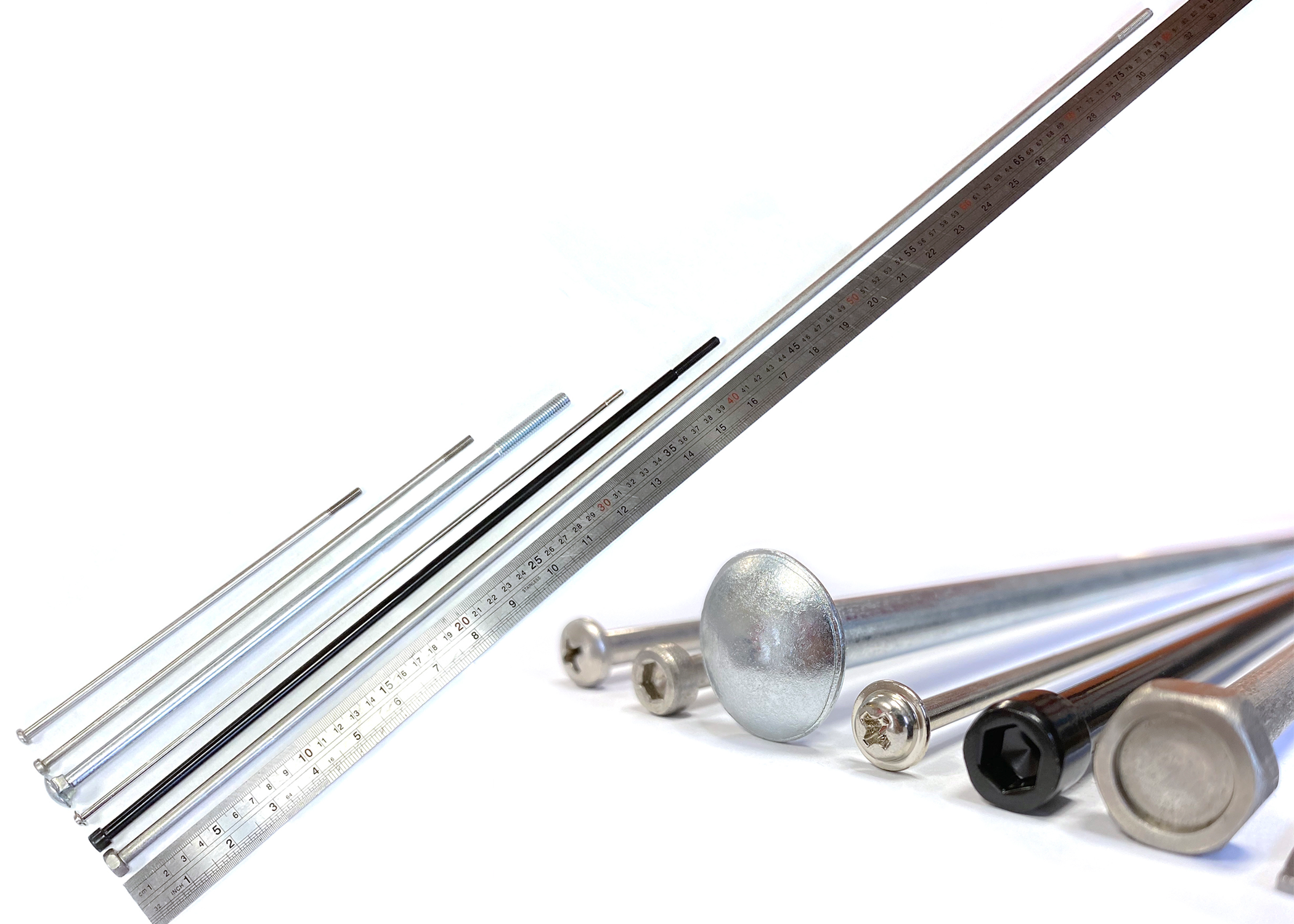
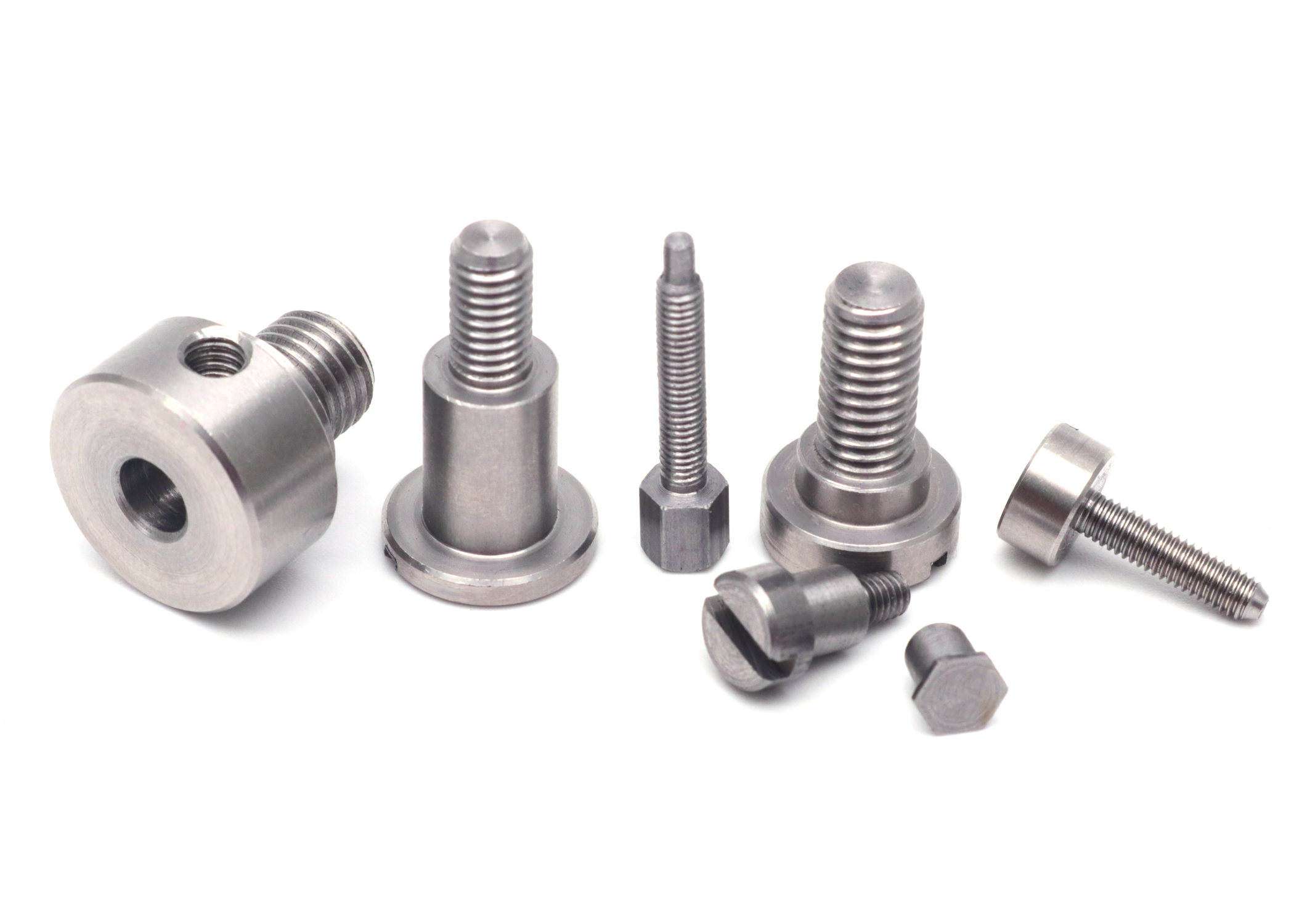
Build Your Custom Solution in 3 Steps
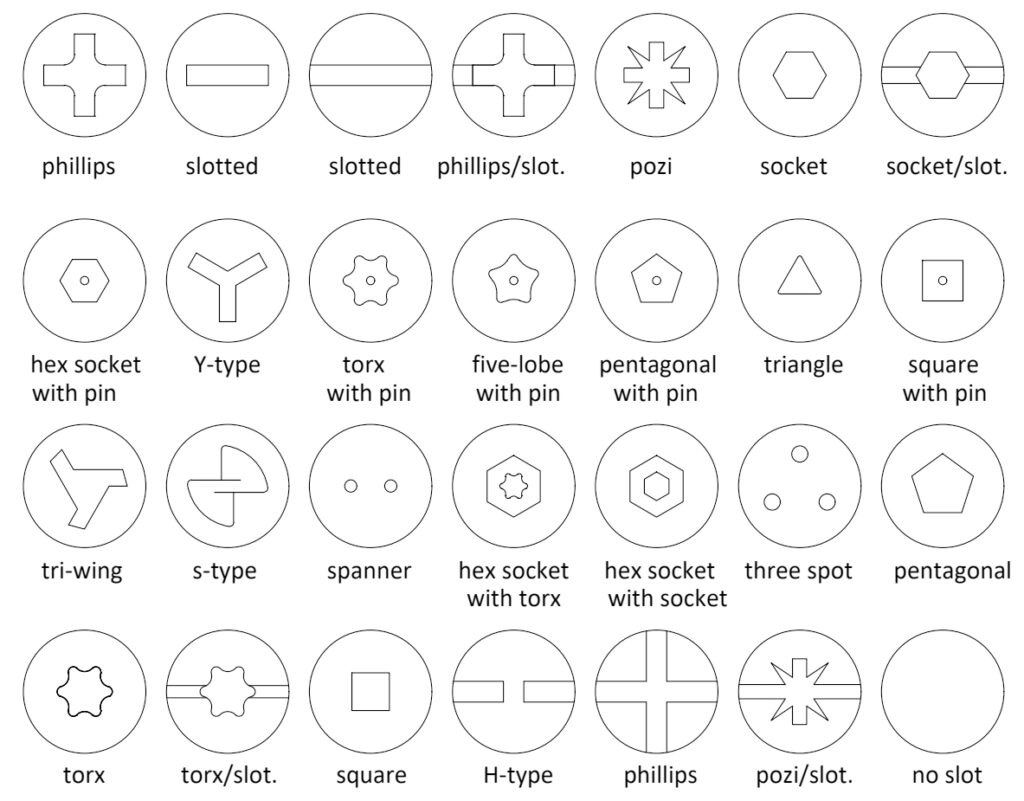
1. Select Your Groove Type – Optimize for Strength or Flexibility
Choose from 10+ engineered groove profiles – from standard V-grooves for general applications to specialized T-slots for heavy machinery.
Our CNC machining ensures ±0.005mm tolerance for perfect load distribution.
Pro Tip: 90% of industrial clients select helical grooves for vibration resistance.
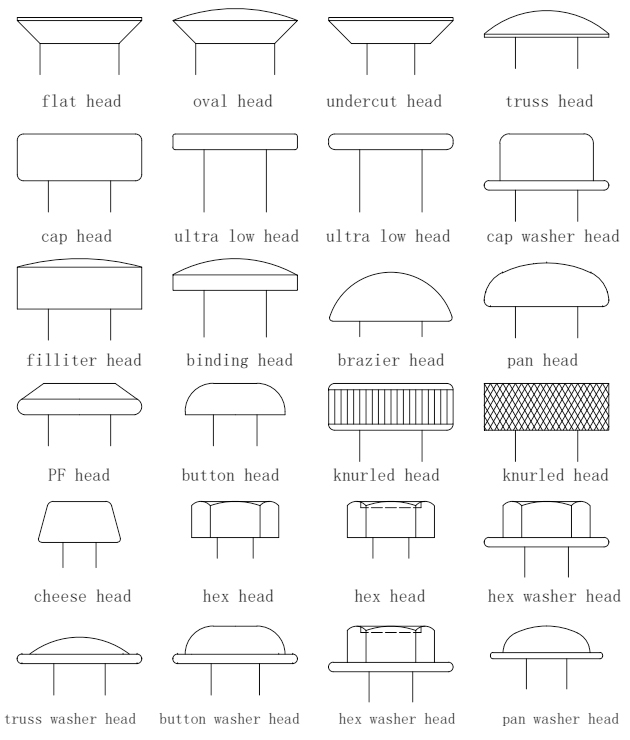
2. Choose Tooth Type: Precision Cutting or Smooth Engagement
Select triangular teeth for high-speed cutting (ideal for aerospace alloys)or rounded teeth to reduce wear in repetitive assembly (common in automotive).
Custom tooth pitch options available – Our engineers recommend 2.5mm pitch for 80% of polymer applications.
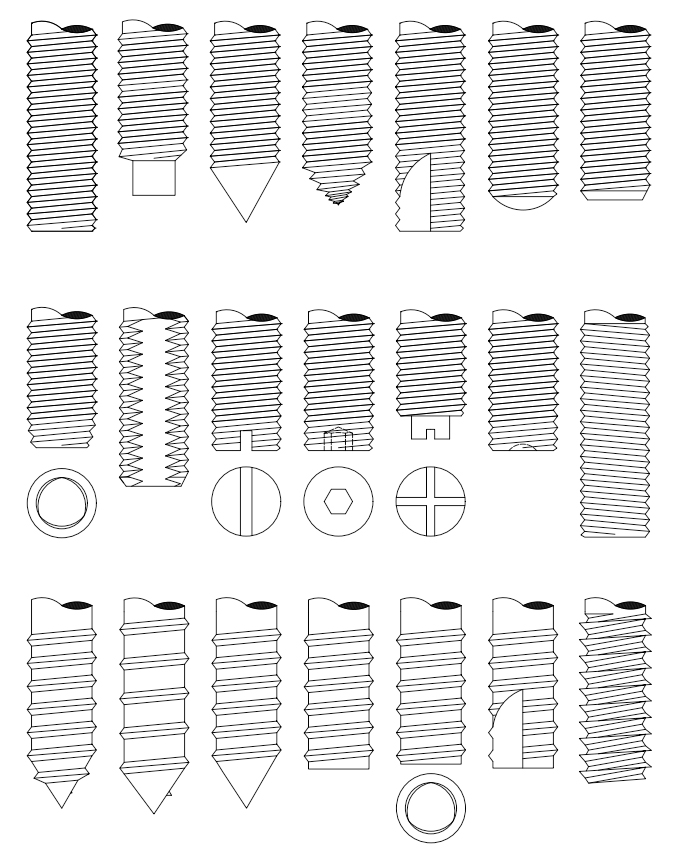
3. Design Your Head Shape: Functional Aesthetics Meets Installation Efficiency
From low-profile hex heads (ISO 4762) to tamper-resistant Torx designs, select shapes that align with your tooling ecosystem.
Pro Tip: 70% of clients pairing button heads with recessed grooves reduce installation time by 40%.
Precision-engineered from concept to delivery: Streamlined 5-stage process with 1-hour response, 72h prototyping, and ISO-certified quality control.
1.Upload Drawing
Submit CAD/PDF drawings or send samples online.
2. Your request
Shape, material, surface finish, quantity, size。
3. Rapid Prototyping
CNC precision machining + 3D printing synchronous start-up, 72 hours to deliver functional samples。
4. Provide a report
To provide you with a customized product inspection report and production cost forecast.
5. Mass Production & QC
The whole process of digital production, every 500 pieces of full inspection once, support SGS third-party inspection, 7-15 days to complete order delivery.