Titanium screw full-scene customization expert
✅ Medical Compliance: ISO 13485-ready, RoHS/REACH reports
✅ Zero Rust: Anodized/Micro-Arc Oxidation, 96-120H salt spray (MIL-STD)
✅ Extreme Environments: -200°C to 600°C stability
✅ Rapid Customization: CNC machining for complex geometries (±0.03mm)
✦ 37+ Yrs Expertise ✦ Batch Traceability ✦ 48H Prototype”
Product Presentation
Have you encountered any of these problems?
Nobody takes orders for titanium screws
Existing supplier technology is not up to standard
Limited surface treatment
Suppliers can not meet the process
The quality fluctuates frequently
Forced to switch suppliers repeatedly
Our solution
Material Breakthrough → full coverage of titanium
Cold heading TA1/Ta2 + turning TC4 precision parts
Medical quality control →99.8% yield
SGS/ROHS/ISO13458 certification
Special material covering → military grade metal customization
C17200 beryllium copper/A286/titanium etc. 20 + special materials, with material report
Customize the solution according to your needs?
Why Us?
Extreme lightweighting
30% weight loss, + 15% range
(aerospace/high-end bicycle screw steel → titanium, density 4.5 g/cm3)
Implant-grade security
Knee implants 0 rejection, titanium allergy rate < 0.6%
(orthopaedic screws/surgical instruments, ASTM F136 certification)
Shield under extreme conditions
Geothermal well screws are acid and alkali resistant + 450 °C thermal corrosion
(energy drilling/industrial furnace, continuous over-service)
Corrosion Terminator
Nuclear power plant valve body screw 0 corrosion, maintenance-free life increased to 5 years ↑
(offshore platform/chemical equipment, salt spray resistance 1000h +)
Magnetic resistance to high temperature
MRI device 0 magnetic interference | jet engine 800 °C strength
(medical imaging/aero-engine fasteners, better than aluminum soften 300 °C)
What are the areas of application?
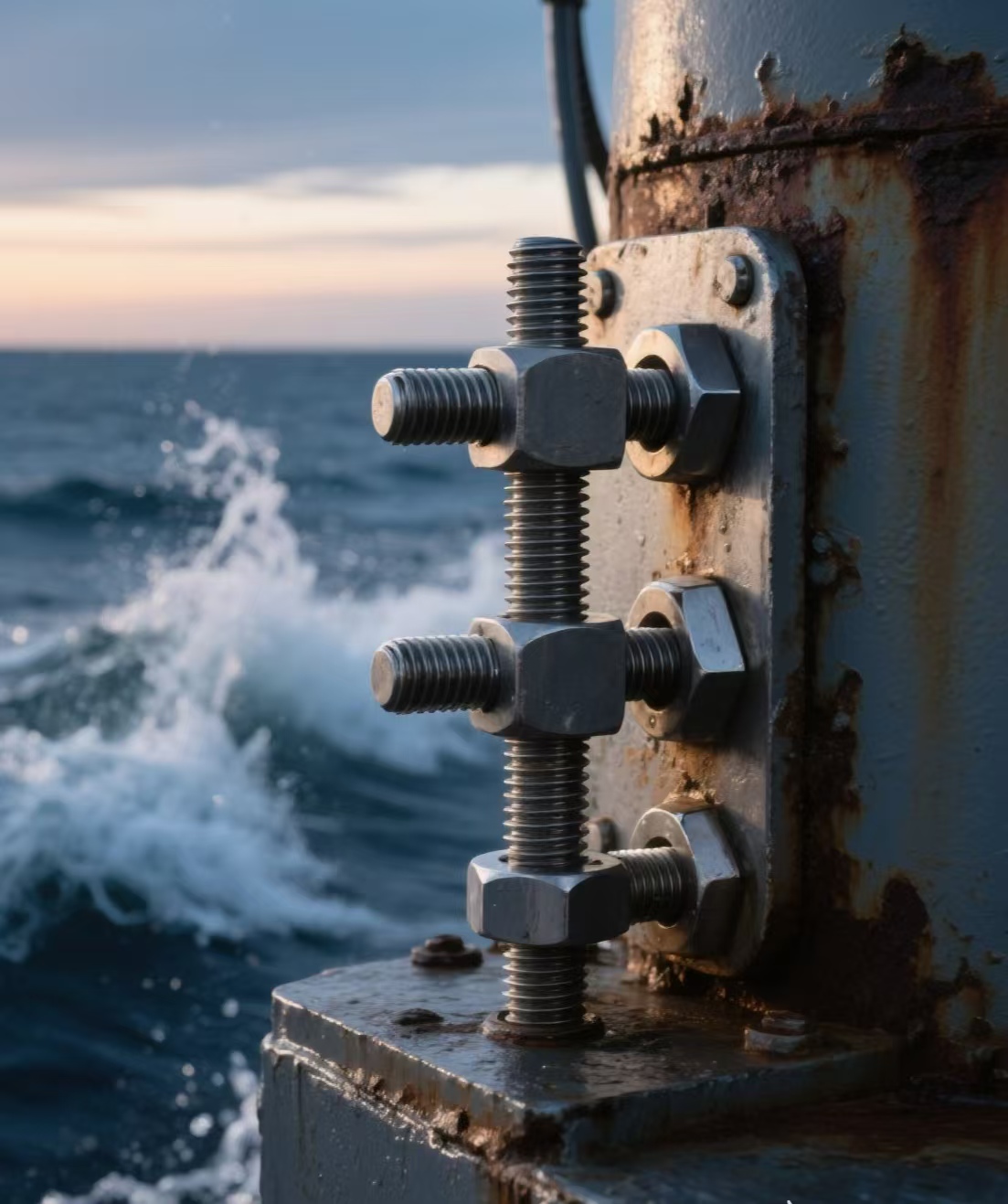
Naval equipment
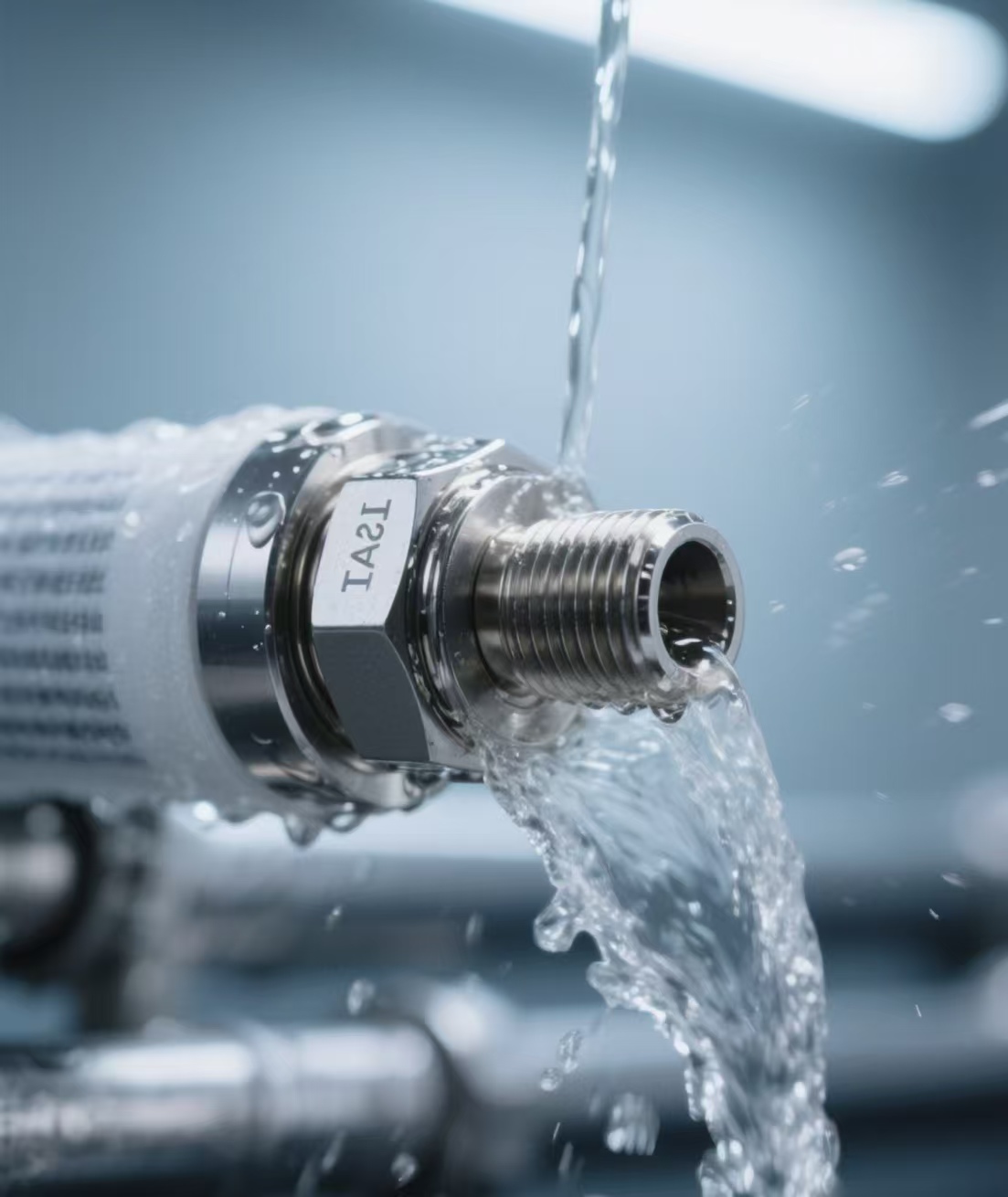
Water purification equipment
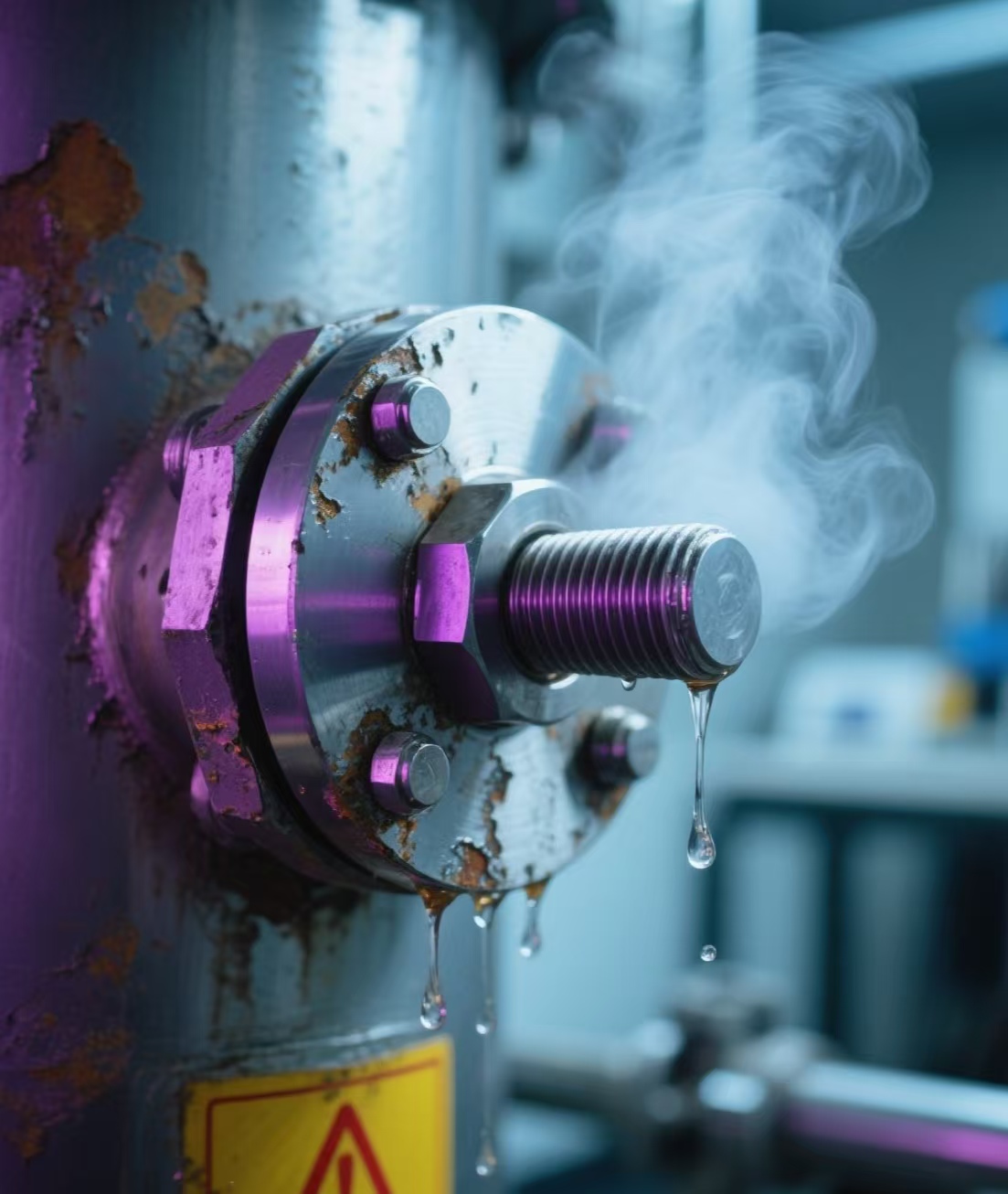
Chemical equipment
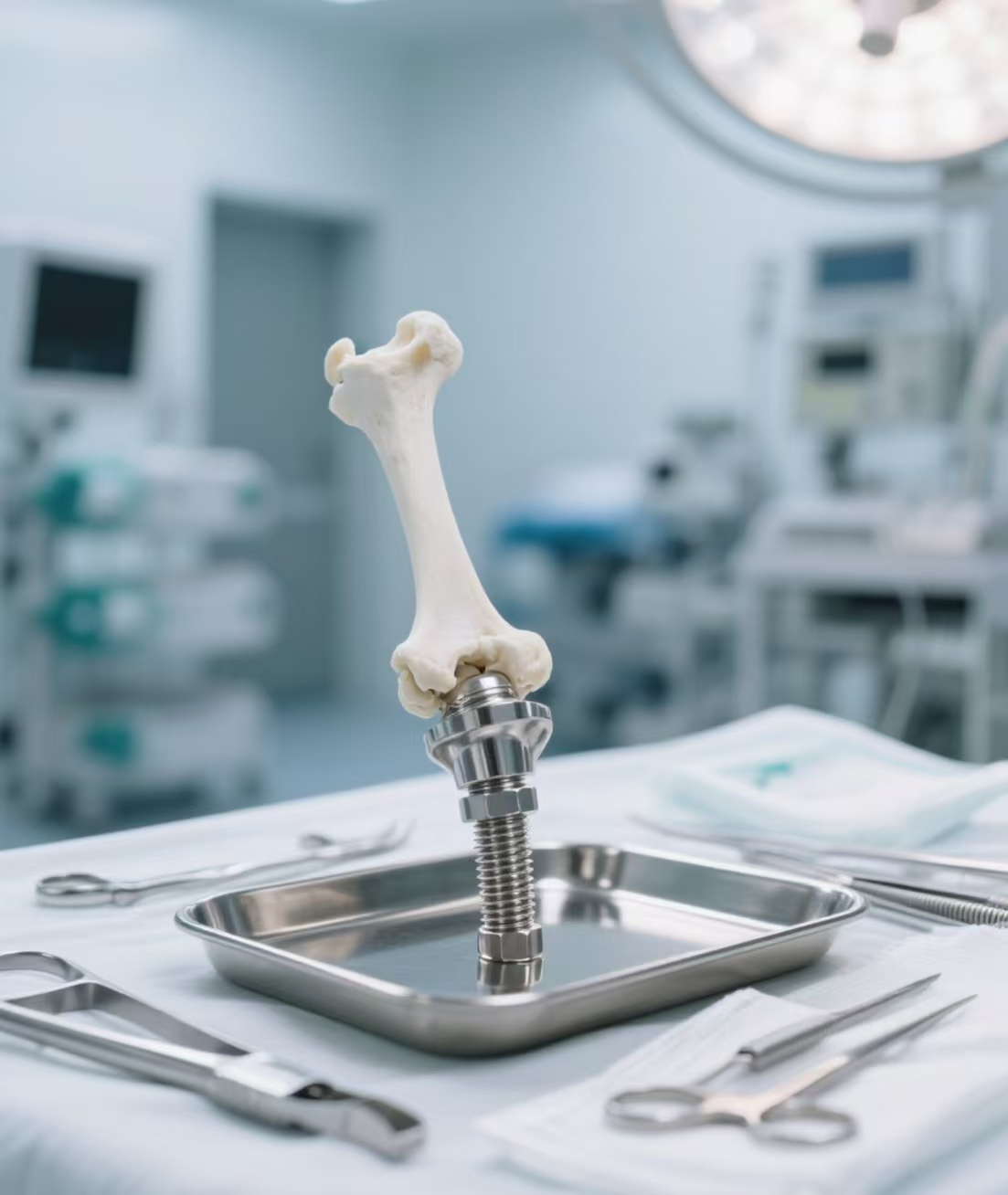
Medical equipment

Smart home
Our certificate
Our Happy Clients!
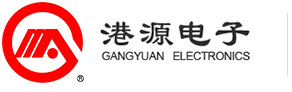
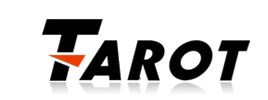
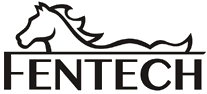
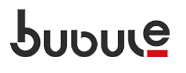
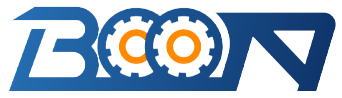
Customize the process
01
Pre-screening of requirements
Lock size/material/finish/quantity
02
Reinforcement by design
Anti-fracture scheme: groove depth optimization | r angle reinforcement | half tooth anti-loosening
03
Transparent quotation
The process is difficult to quantify and the cost is reduced by 20%
04
Full Price Production Schedule
0 deposit advances, the collection will start
04
Full Price Production Schedule
0 deposit advances, the collection will start
05
Production of military grade
99.8% yield + full inspection of stop gauge
06
Certified Delivery
SGS with goods | delay by day
Frequently Asked Questions
Triple Line of defense
Biocompatible Iron Certificate: ASTM F136 certified, clinical allergy rate < 0.6% (far exceeding ISO 5832-3 standard)
Zero pollution production: 10,000-class dust-free workshop, 100% complete check of implant screw stop gauge
Fatal scenario test: salt spray 1000h | Hydrogen embrittlement test | 800 °C strength retention report (with original data)
Iron Law of military grade delivery
Urgent medical order: 72 hours to deliver orthopaedic implant screws (routine 15 days)
Depth of custom parts: 7 days of shipment (peer average 30 days)
Compensation for overdue date: 2% of the contract amount over 1 day, 30% of the maximum (written into the contract)
Technology: cold heading pure titanium capacity margin: TA1/TA2 threads M1-M12
Technology: Turning Titanium alloy capacity boundary: TC4 precision parts ± 0.01 mm
Technology: micro-arc oxidation capability boundary: Military Gray/deep space black (GB 96H +)
To cover the territory
Medical:ISO 13485|FDA 510(k)|CE MDR
Military industry: NADCAP | AS9100D | GJB
Industry: ISO 9001 | PED 2014/68/E U | Canada CRN
Scenario: orthopaedic implants, hidden cost: $12,000 for second exclusion + titanium option value: 30 years 0 exclusion, Zero Cost
Scenario: desalination, hidden cost: annual corrosion maintenance $8,000 titanium solution value: maintenance-free life > 10 years
Scenario: aero-engine, hidden cost: 1g weight loss = $300 fuel/year titanium solution value: 50% weight loss year-on-year, $150,000 annual savings